Rethink the Rack: Alternatives to Selective Racking Can Optimize Your Existing Space
Posted on Oct 21, 2024
Lease rates for commercial and industrial buildings are primarily based on the square footage of a building’s footprint, but when it comes to warehouses and distribution centers, cubic footage is a far more important number. That cubic footage also presents the opportunity for storage facilities to become more productive, taking advantage of racking systems that optimize the use of vertical space.
In most cases, that means moving away from the traditional “selective” racking, which offers direct access to products without having to move pallets or tote containers. That single-deep racking might be convenient for handling certain products, but a large amount of floor space is needed for aisles to access items.
“We’re at a point where selective racking isn’t necessarily the obvious path anymore,” says Craig Heil, Specialty Products Manager at Steel King Industries. “Once companies start considering how to store more pallets in their facilities and make better use of vertical space and/or move goods through facilities faster, alternative racking options start to look a lot more suitable and compelling,” he adds.
That’s especially true when a facility operator can’t increase floor space square footage, or move to a larger facility.
Selective racking alternatives condense the loads and reduce distances needed to travel to access products.
“With selective racking, you may have to pass 20 bays to get to the pallet you need,” says Ryan Wachsmuth, Steel King’s Southeast Regional Sales Manager. “Whereas dynamic and high-density options allow you to ‘condense’ the rack footprint and put product within closer proximity.”
If you’re looking to get more out of your warehouse or DC, may it’s time to “rethink the rack” to maximize material handling efficiency.
Selective Racking Alternatives
As noted in a Steel King whitepaper published by Modern Materials Handling, there are three main alternatives to selective racking – each with specific benefits that offer solutions to various needs. Those include pushback racking, pallet-flow racking, and semi-automated racking systems. Following is a brief look at the structure and benefits of each type. To learn more, see the whitepaper.
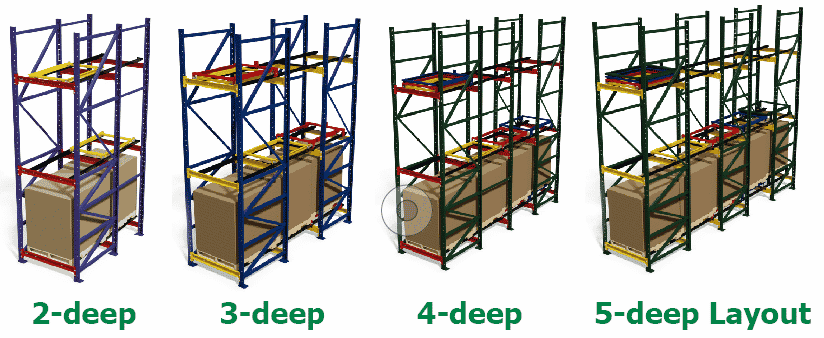
Pushback Racking
Pushback Rack Systems
In pushback racking systems, each pallet load is placed on a nested cart which rides on inclined rails. That load pushes back the previously placed pallet load. When a load is removed, the other pallets in that bay roll forward, so there is always a pallet load in the front row. With access only at the front of the rack, these selective racking alternatives are “first in, last out” applications. Pallet loads can be two to five deep.
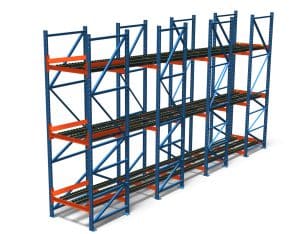
Pallet Flow Racking
Pallet Flow Systems
In these systems, products are loaded on one side of the racking and removed on the other side. Pallet loads are placed on inclined rails that allow the load to flow to the unloading side. Thus, these systems allow for “first in, first out” product handling, which is critical for items that are perishable or that have “use by” dates. Each bay can be two to 30 pallet positions deep.
Semi-Automated Systems
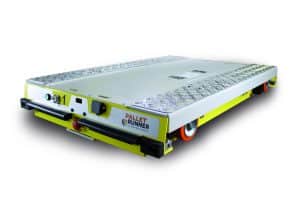
Semi-Automated Pallet Shuttle
These systems rely on some level of automation, such as Steel King’s Pallet Runner that moves a pallet load into position once it is placed in the racking. Because the Pallet Runner is automated, deep lanes of storage are possible, maximizing use of a facility’s cubic space and reducing labor needed for load handling. The Pallet Runner can be programmed to leave space between pallet loads to address fire prevention codes and insurance company mandates.
Choosing the Right Selective Racking Alternative
Replacing selective racking with one of the above systems requires thorough planning and input from all stakeholders, Steel King’s Wachsmuth notes.
“Talk to the forklift drivers who will be loading and unloading the system,” he says. “They are often the best source of input and feedback on what’s going to work for your specific application.” Input also should come from maintenance personnel, facility managers and C-level executives, he adds. And just as important is information from your insurance company and local municipality regarding codes.
Through those discussions and research, you might find that an alternative to selective racking will let you remain in your existing space, but with much better material handling efficiency.