Fire Prevention Plays Key Role in Racking Design
Posted on Oct 29, 2024
Storage racking systems are generally designed to hold certain types of commodities; however, warehouse fire protection codes and standards also play a big role in the design. Those requirements and guidelines can be complicated and can be imposed in some locations while not others. Application of one aspect of warehouse fire prevention can have implications for other aspects.
So, where do you start in addressing warehouse fire prevention? The best option is as soon as possible, because fire codes take precedence in how a building and the equipment within is designed.
“Fire protection isn’t one thing – it’s a multi-faceted package that’s tailored to a specific racking system within a specific building within a specific municipality,” said Jerry Schultz, a fire protection engineer and owner of The Fire Protection International Consortium. “When the racking system is designed to meet fire-related codes and when the building itself complies with protection codes (the package), you get a safe building,” Schultz notes.
The “package,” however, could include aspects that are not required by code, such as the use of early suppression, fast response (ESFR) sprinklers, which Schultz called “extremely powerful” in their effectiveness. ESFRs can apply more than three times as much water as standard sprinklers, and have other benefits such as the fact that, when used, heat and smoke vents are not required, in-rack sprinklers are typically not required and, perhaps most of all, the ESFR sprinkler provides great flexibility in what commodity it can protect. The concern with smoke and heat vents, he says, is that they could cause the wrong ESFR sprinklers to activate, e.g. those not in the fire area. Due to the lack of smoke and heat vents and the ability to protect multiple commodities or racking arrangements, ESFR sprinklers are becoming standard in spec-built warehousing.
Alternatively, Control Mode Density Area (CMDA) sprinkler systems, which were the industry standard for warehousing, are used in conjunction with smoke and heat vents. These sprinklers are intended to control fires where the density-per area criteria is used for storage. There are other sprinkler types that are appropriate for use, depending on a facility’s design and the commodities being stored.
The codes have recently been revised to require fewer smoke and heat vents. It is critical to know what edition of the code is being enforced by the municipality. It used to be 4×8-foot vents every 2,400 square feet.
Flue Type and Placement a Key Component
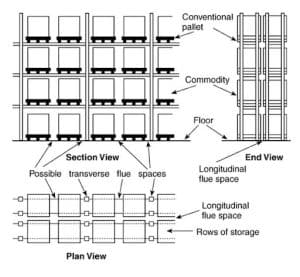
Warehouse Layout Diagram
NFPA and Factory Mutual define two types of flues: longitudinal – which is the space seen from the end of the aisle and runs in the down-aisle direction, and transverse – which is the space seen from within the aisle and run in the cross-aisle direction. Codes for fire prevention warehouse racking generally require vertical flue space within racking to allow heat from a fire to rise and trigger a sprinkler, and then to allow the flow of water from the fire sprinkler to flow down through the rack. If racking is classified as having solid shelving, in-rack sprinklers are needed. This “solid shelving” definition play a role in determining whether flues are required or not.
“Solid Shelving” Definition Impacts Flue Placement
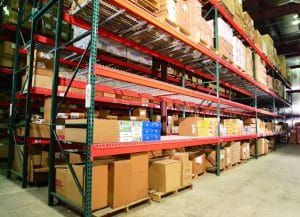
Solid Shelving
Solid shelving is defined as shelving that is fixed in place and that has a slatted, wire mesh or other type of surface within the racks. The area of a solid shelf is defined by the perimeter aisle or flue space on all four sides, or by the placement of loads that block openings that would otherwise serve as the required flue spaces. Solid shelves with an area equal to or less than 20 square feet are defined as “open” racking. Shelves of wire mesh, slats or other material more than 50 percent open, and where the flue spaces are maintained are also defined as “open” racking.
For fire prevention for warehouse racking, the flue requirements are based on the number of rows. Single-row racking does not need a longitudinal flue space. For double-row racking up to 25 feet top of storage, no longitudinal flue is required while transverse flues are required at uprights and between loads. But, in double-row racking, if longitudinal flues are provided and there are transverse flues every five feet, the racking is not considered solid shelving. For double-row racking more than 25 feet top of storage, both longitudinal and transverse flues are required.
Multiple-row racking is not considered solid shelving if both transverse and longitudinal flues are provided. Loads can’t be butted up against each other; a longitudinal flue is needed every five feet. But an exception is offered: a longitudinal flue is not required if a transverse flue can be added every five feet, and the rack depth is not greater than 20 feet and 3.5-foot aisles are provided (although Factory Mutual requires eight-foot aisles.) between back-to-back groupings.
For more information on rack design in regard to warehouse fire precautions, check out this blog from Steel King dealer Cisco-Eagle.
Do Totes Circumvent Fire Suppression?
Noting an increased use of totes and bins to hold commodities in racking systems, Schultz notes a problem with their use for warehouse fire prevention: in that they collect water when fire sprinklers are activated, greatly lessening the sprinklers’ ability to suppress a fire. To alleviate that problem, he recommends that totes be covered so they would not collect sprinkler water. But he also notes that a recent material handling trade show an exhibitor recommended drilling holes in the bottom of the totes to allow water to flow through.
Codes Don’t Address ASRS Systems
Though not covered by current fire codes, another racking area of growing importance are fire suppression requirements relating to automated storage and retrieval systems (ASRS) in which commodities are tightly packed. Theoretically, if there were a fire in an ASRS, where compactness makes the use of sprinklers non-feasible, fire-fighting crews would have to tear down walls to reach the affected area. While not covered by code, fire protection guidelines for ASRS systems are addressed by FM Global, a major building insurer.
Most jurisdictions in the U.S. have adopted the International Building Code and its fire protection provisions which reference NFPA 13 of the National Fire Protection Association. But a local jurisdiction’s code could include the International Building Code, state, county and local municipality, the International Fire Code, and various NFPA standards in addition to NFPA 13 which deals with sprinklers.
Then there are the FM Global Property Loss Prevention data sheets, which can differ from established codes and as noted above, are alone in addressing ASRS systems. The updated NFPA standard for sprinklers, NFPA 13, is due out this fall but still does not provide ASRS requirements, so FM Global remains the go-to reference. (The data sheets are free to download at FM Global’s website.)
Do Code Changes Affect Existing Structures?
We’ve discussed the importance of incorporating fire suppression systems in distribution centers and warehouses, but what happens when the code changes, which happens every few years?
“In general, changes to codes are not retroactive,” Schultz notes, “so there is no need to inspect a facility every three years regarding compliance with the updated IBC; however, facilities should be reviewed and inspected with some regularity.” NFPA 13 states that “the provisions of this standard shall not apply to facilities, equipment or installations that were existing or were approved for construction or installation prior to the effective date of the standard.”
But there is an exception, with the NFPA standards stating that the AHJ (authority having jurisdiction) can determine that an existing situation presents an unacceptable degree of risk, so the AHJ can mandate that new standards can be applied retroactively if the risk to safety is too high in their opinion.
The AHJ is not one person. At any given point, it could be the plan reviewer, a municipal building code official, the fire department, the insurance company, the engineer of record, a fire safety consultant, or others.
Other Significant Factors in Safety Compliance
- Travel Distance: IBC coding relating to the distance building occupants need to travel to get out in the event of a fire had been 400 feet and then changed to 250 feet, but if there’s a place for smoke to go, the 400-foot distance could be authorized.
- Fire Department Ingress: Racking generally is not allowed above an emergency entrance for fire fighters.
- Fire Alarms: Most codes do not require fire alarms for a storage occupancy building. A local municipality could require them.